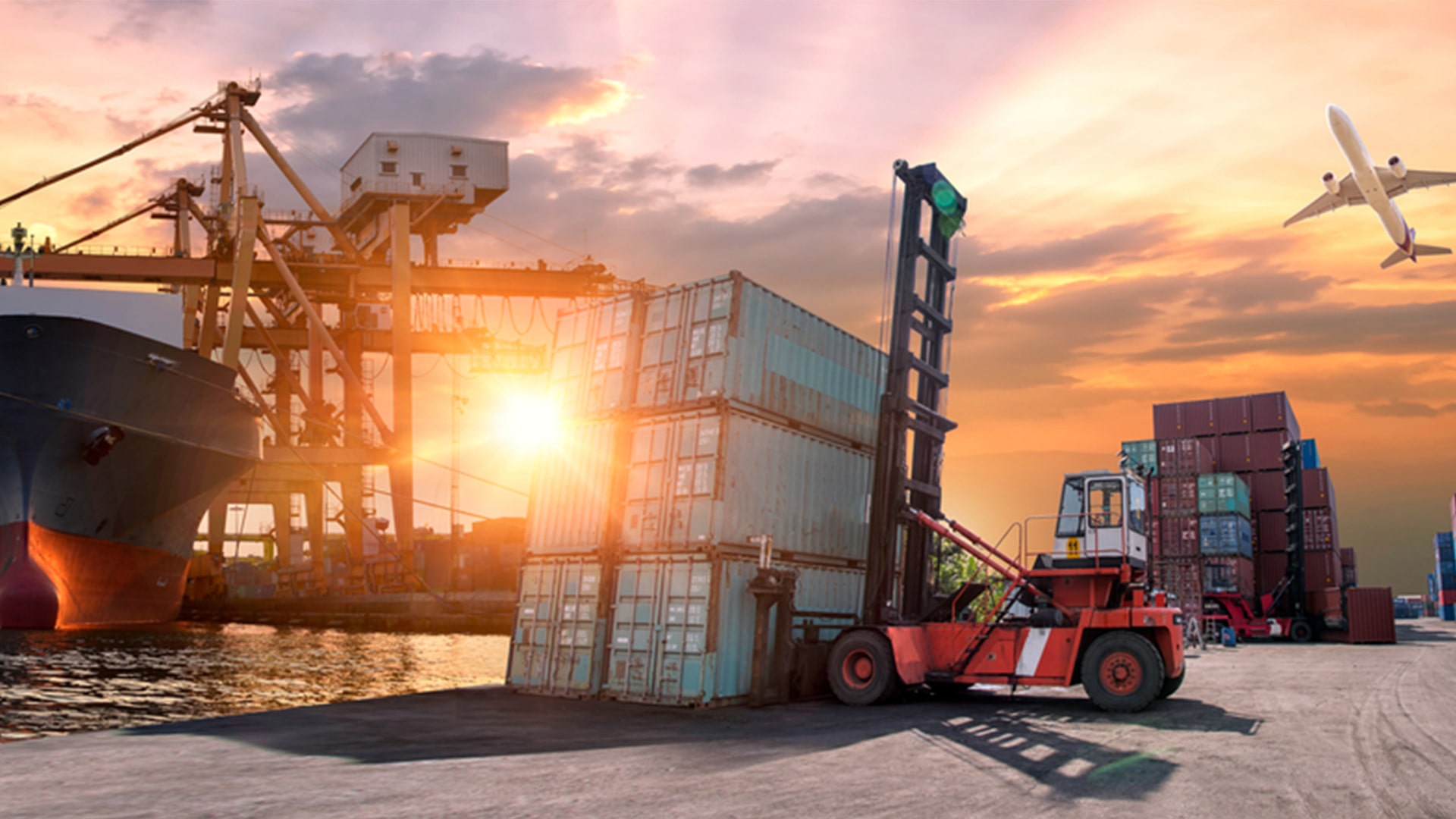
How to Create a Supply Chain?
Supply chain is a network of processes that includes all stages from the production of a product or service to the end user. Creating a supply chain can be a complex process because it involves many different components, suppliers, manufacturers, distributors and retail points. Here are the basic steps you need to consider when creating a supply chain:
- Planning and Strategizing
Determine your goals, market and customer demands before creating your supply chain.
Plan which stages your supply chain will include, where your products will be produced and how they will be distributed.
- Supplier Selection
Research and select reliable suppliers who will provide the materials or services you need.
When choosing a supplier, consider factors such as price, quality and delivery times.
- Production and Product Development
Create a manufacturing process that will produce your products or deliver your services.
Determine product design, production methods and quality control processes.
- Distribution and Logistics
Establish an effective logistics network to deliver your products to customers.
Plan elements such as storage, transportation, inventory management.
- Inventory Management
Create an effective management system to keep your product inventory under control.
Consider factors such as demand forecasts, inventory levels and order management.
- Data and Information Management
Establish data collection and analysis systems for traceability of all processes in your supply chain.
Optimize your decisions with real-time data analysis.
- Risk Management
Identify risks that may occur in your supply chain and create plans against them.
Consider factors such as supplier delays and natural disasters.
Collaboration and Communication
Establish processes to ensure effective communication and collaboration between all stakeholders in the supply chain.
Information sharing and collaboration ensure the efficient functioning of the supply chain.
- Continuous Improvement
Regularly evaluate the performance of your supply chain and make continuous improvements.
Demonstrate flexibility to adapt to changing market conditions.
Creating a supply chain can vary depending on your industry, business model and goals. Professional advice, technological solutions and industry standards can help you in this process. Remember, supply chain management requires continuous effort and processes must be optimized over time.
What Does Supply Chain Include?
Supply chain is a network of processes that includes all stages from the production of a product or service to the end user. The supply chain includes various components and activities and generally includes the following key components:
Suppliers: Companies or individuals that provide materials, parts or services. It is the beginning of the supply chain.
Manufacturing: It is the stage where products or services are physically produced or created. At this stage, products may be assembled, processed, or services may be offered.
Logistics and Distribution: It covers the process of storing, transporting and distributing products. Warehouse management includes activities such as transportation planning and shipping.
Inventory Management: It includes the operations carried out to control the stock levels of products or materials and optimize the inventory.
Demand Forecasting and Planning: These are the activities carried out to predict customer demands and plan production and supplier processes according to these demands.
Product Development and Design: It includes the phase in which new products or services are designed and developed.
Sales and Marketing: It covers the stage where products are marketed, sold and delivered to customers.
Customer Service: Includes activities carried out to ensure customer satisfaction, solve problems and respond to customer demands.
Recycling and Waste Management: It includes recycling or proper waste management processes when the products' life ends or waste is generated.
Data and Information Management: It covers the phase of managing, analyzing and using the data collected throughout the supply chain to make the right decisions.
Risk Management: It includes activities carried out to identify, evaluate and take measures against potential risks in the supply chain.
Collaboration and Communication: It includes the work done to ensure effective communication and cooperation between all stakeholders.
Supply chain management works efficiently by integrating and coordinating these components with each other. Developing the right strategies and processes at every stage ensures the success of the supply chain.